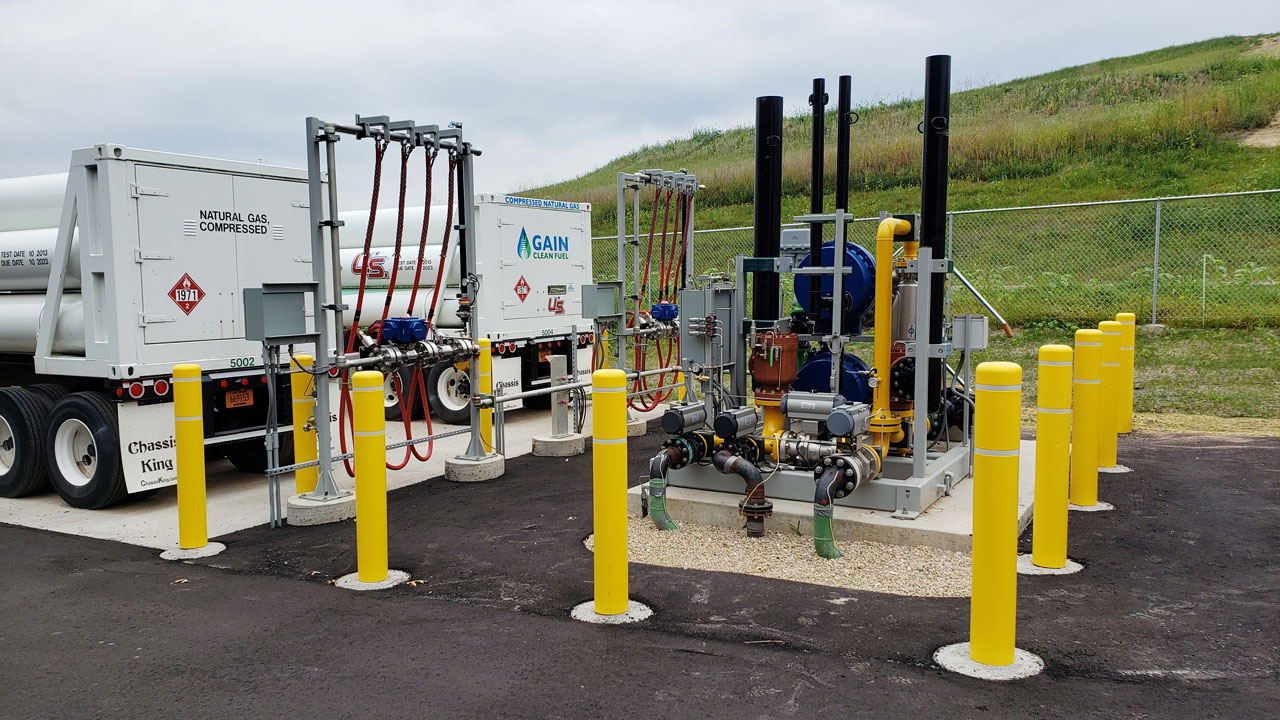
Tetra Tech’s Ben Peotter and Dane County, Wisconsin’s, Mike Wyrick discuss a novel renewable natural gas (RNG) offloading station concept that helps biogas producers gain access to the pipeline, renewable energy markets, and other U.S. federal and state credits.
Information from this industry insight was originally published in Waste Advantage Magazine.
The Dane County Department of Waste & Renewables operates a state-of-the-art RNG processing facility that converts an adjoining landfill’s biogas into pipeline quality natural gas and injects it into a nearby interstate pipeline. The RNG facility also includes a virtual pipeline station that enables agribusinesses, like Wisconsin dairy farm manure digesters, to transport their gas to the Dane County facility for offloading and pipeline interconnect. This novel offloading station is the first project in the United States to certify several pathways and feedstocks at the same time.
But, like many new ideas, the trailblazing project was not without challenges. Here we highlight lessons learned from integrating all the necessary mechanical, electrical, and control systems. Projects like these are becoming more common, so these post-project lessons may help others identify and avoid some of the issues faced by the Dane County project.
Meeting Design, Construction, and Commissioning Challenges
The County faced several unanticipated challenges, including the need to design the facility within a small site footprint while still optimizing site access, a compressed timeline, and wide pressure and temperature ranges. It also requires the integration of controls across vendor-supplied equipment packages and coordinating complex elements with municipal staff acting as the project coordinator and project owner. Perhaps the most unique design challenges were posed by the need to navigate the extreme temperature drop realized when a trailer is unloaded at a rapid rate. A portion of the offloading station infrastructure had to be designed to handle temperatures as low as -100 °F.
Lessons Learned
Lesson #1: Know Your Customer
It may seem obvious, but the first thing anyone hoping to develop a remote offloading system for digester gas should know is, who is your customer? RNG owners, operators, gas transporters, and gas and credit marketers each have different goals and requirements. Identify and communicate with those who make the decisions for operational, technical, commercial, and regulatory issues. Use this information to develop a scheduling plan and a reporting system that maximizes offloading given customer constraints.
Lesson #2: Know Your Customer’s Trailers
Repeat after us: trailer build matters! Using a trailer outfitted with traditional Type 1 steel storage cylinders versus Type 4 composite cylinders found on the largest trailers will have major impacts on engineering, operation, and economics. Proper engineering and operations planning requires accurately understanding trailer specs upfront, so you are sure to respect different temperatures, pressures, and flow limits unique to each trailer type. The wrong trailer type can restrict a system and reduce the number of customers the facility can serve.
Lesson #3: Pay Careful Attention to Designing for Low Temperatures
Systems developed for use in low temperatures face important design, operation, and business case considerations. For example, rapid offloads (1-2 hours) in winter (~30 °F for Dane County) may result in more product gas left on the trailer than planned. Sizing any trailer offloading station requires a thorough understanding of temperature and pressure limitations; otherwise, system restrictions may result in trailers offloading at a slower rate than planned. The more rapidly a trailer is unloaded, the lower the temperature of the RNG will drop and, as a result, equipment may freeze. Proper planning and inclusion of infrastructure specifically designed to operate at these potentially extremely low temperatures can often mitigate these issues.
Lesson #4: Develop Specific Low Temperature Operations Plans
Expect and plan for failures and challenges during winter. Systems should be rated down to a temperature of at least -65 °F. Though RNG facilities at digesters will be designed to meet the pipeline tariff moisture limit, even the very small amount of residual water in the gas may freeze due to the rapid temperature drop during offloading. Stricter moisture limits on the digester agreements may alleviate some of these concerns. In some cases, it might make sense to invest in a gas dryer on the digester side to maximize the trailer offload rate.
Lesson #5: Tips on Systems and Parts
RNG compression and unloading systems must be capable of operating across a wide range of temperatures, pressures, and flow rates, so of course safety is of paramount concern. When operating a system at pressures greater than 4,000 pounds per square inch (PSI), any failures have the potential to be catastrophic and cause injury and death, in addition to the damage or destruction of expensive and specialized infrastructure. Adequate safety equipment, including pressure relief valves, accurate real-time pressure and temperature monitoring, and gas detection devices is a project necessity.
It’s also important to have a good understanding of the supply chain and associated vendor lead times. Anyone looking to develop a project should expect lead times of at least 24 to 36 weeks for most equipment, with some systems approaching or exceeding one year. Once a facility is operational, it is imperative to maintain a stock of critical spare parts. Remember, downtime equals lost revenues.
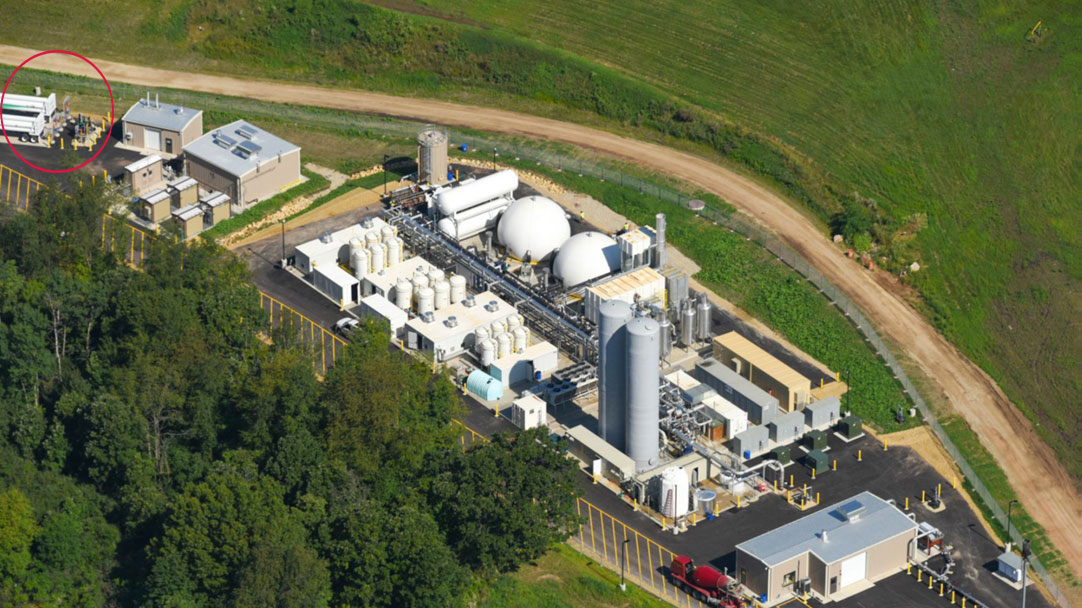
Planning Leads to Successful Implementation
As the Dane County project evolved, the team identified numerous specific technical issues inherent to the trailer rapid offloading. They also had to continually overcome challenges that arose associated with specific design elements of the two distinct systems. Ultimately, the County managed these technical and operational constraints and operates a successful system that could be an implementation model for other regional injection sites.
About the author
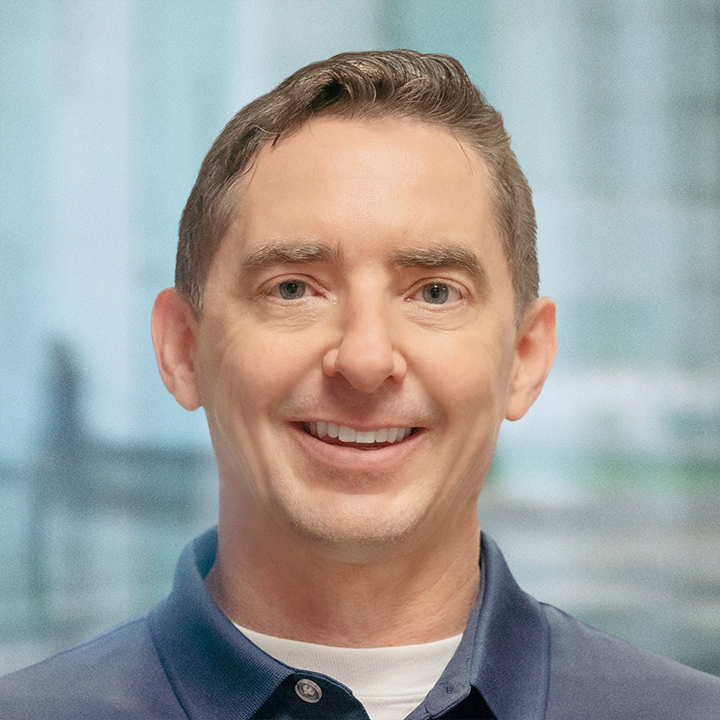
Ben Peotter
Ben Peotter is a client manager for solid waste and renewable services.
He has been a professional environmental engineer and innovator in the solid waste and renewable energy industry for more than 25 years and has been involved with U.S. biogas resources development projects since 2004.
Ben has served as client liaison and project manager and successfully completed project elements for solid waste, energy, biogas, environmental, and brownfield redevelopment projects. He has presented at numerous conferences and industry events, including for the Solid Waste Association of North America (SWANA), American Planning Association, the National Recreation and Park Association, and U.S. Environmental Protection Agency.